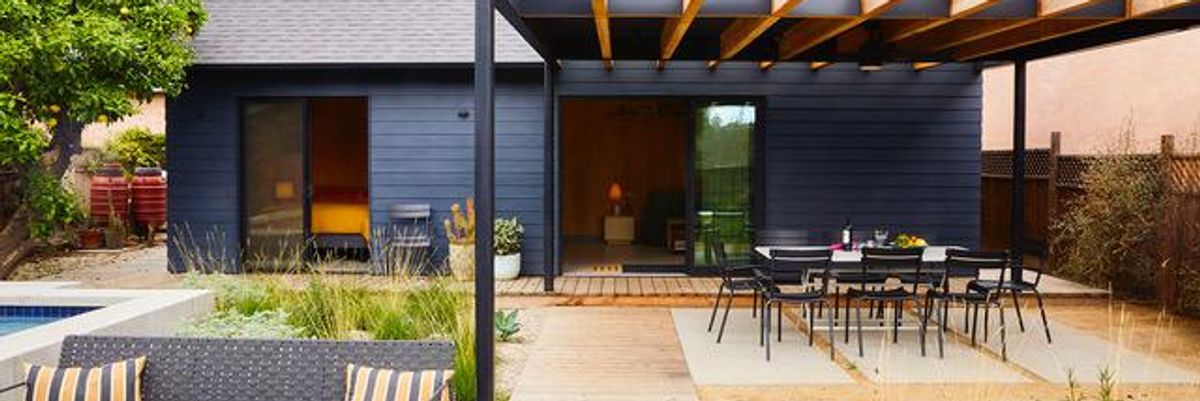
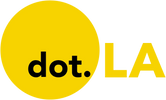
Get in the KNOW
on LA Startups & Tech
X
Design, Bitches
Looking to Build a Granny Flat in Your Backyard? Meet the Firms and Designs Pre-Approved in LA
Sarah Favot
Favot is an award-winning journalist and adjunct instructor at USC's Annenberg School for Communication and Journalism. She previously was an investigative and data reporter at national education news site The 74 and local news site LA School Report. She's also worked at the Los Angeles Daily News. She was a Livingston Award finalist in 2011 and holds a Master's degree in journalism from Boston University and BA from the University of Windsor in Ontario, Canada.
Adding a backyard home in Los Angeles is now nearly as easy as buying a barbecue.
Homeowners who for years have wanted to build a granny flat in their backyard, but dreaded the red tape, can now choose from 20 pre-designed homes that the city has already approved for use.
The shift, made official last week, will speed up a weeks-long process and bring more badly needed units to an overpriced market. It also has the potential to elevate the 14 startups and firms building the next generation of homes.
The designs for the stand-alone residences range from a 200-square-foot studio to a 1,200-square foot, two-story, two-bedroom unit. And many of the homes are filled with design flourishes, reflecting the diverse architecture of the city, from a house in the silhouette of a flower to one with a spiral outdoor staircase leading to the roof.
It's no surprise. The program was spearheaded by Christopher Hawthorne, a former architecture critic at the Los Angeles Times and now the city's chief design officer.
The firms are primarily local and startup architecture and design firms, while others are well-known with a history of building granny flats, also know as accessory dwelling units, or ADUs.
The standard plans avoid the Los Angeles Department of Building and Safety's typical four-to six-week review process and can allow approvals to be completed in as quickly as one day.
Some aspects of the plans can be modified to fit a homeowner's preferences. Eight other designs are pending approval.
Mayor Eric Garcetti believes by adding more such units, the city can diversify its housing supply and tackle the housing crisis. Recent state legislation made it easier to build the small homes on the lot of single-family residences. Since then, ADUs have made up nearly a quarter of Los Angeles' newly permitted housing units.
Because construction costs are relatively low for the granny flats – the pre-approved homes start at $144,000 and can go beyond $300,000 – the housing is generally more affordable. The median home price in L.A. County in January was $690,000.
Here's a quick look at the designs approved so far:
Abodu
Abodu
Abodu, based in Redwood City in the Bay Area, exclusively designs backyard homes. In 2019, it worked with the city of San Jose on a program similar to the one Los Angeles is undertaking.
In October, it closed a seed funding round of $3.5 million led by Initialized Capital.
It has been approved for a one-story 340-square-foot studio, a one-story one-bedroom at 500 square feet, and a one-story, 610-square-foot two-bedroom.
The pricing for the studio is $189,900, while the one-bedroom costs $199,900 and the two-bedroom is $259,900.
Amunátegui Valdés Architects
Led by Cristobal Amunátegui and Alejandro Valdés, the firm was founded in 2011 and has offices in Los Angeles and Santiago, Chile. Amunátegui is an assistant professor at the Department of Architecture and Urban Design at UCLA.
The firm designs work in various scales and mediums, including buildings, furniture and exhibitions.
Its one-story, two-bedroom with a covered roof deck 934-square-foot unit is pending approval from the city.
Connect Homes
Connect Homes has a 100,000-square foot factory in San Bernardino and an architecture studio in Downtown L.A.
It specializes in glass and steel homes and has completed 80 homes in California. Its designs have an aesthetic of mid-century modern California residential architecture.
It has two one-bedroom models pre-approved by the city, one is 460 square feet, which costs $144,500 with a total average project cost of $205,000. The other is 640 square feet, which costs $195,200 with a total project cost of $280,000.
Design, Bitches
The Los Angeles-based architectural firm founded in 2010 describes itself as having a "bold and irreverent vision." Its projects include urban infill ground-up offices to single-family homes, adaptive re-use of derelict commercial buildings and renovations of historic landmarks.
Its pre-approved design, named "Midnight Room," is a guest house/ studio. Its bedroom can be left open for a loft feel or enclosed as a separate room. The design is a one-story, one-bedroom at 454 square feet.
Escher GuneWardena Architecture
Founded in Los Angeles in 1996, Escher GuneWardena Architecture has received international recognition and has collaborated with contemporary artists, worked on historical preservation projects and more.
The company has been approved for two different one-story, one- or two-bedroom units, one at 532 square feet with an estimated cost of $200,000 and another at 784 square feet with an estimated cost of $300,000. The firm noted the costs depend on site conditions and do not include soft costs. Those could add 10% to 12% to the total construction costs.
First Office
First Office is an architecture firm based in Downtown Los Angeles. Its approved ADUs will be built using prefabricated structural insulated panels, which allow for expedited construction schedules and high environmental ratings.
The interior finishes include concrete floors, stainless steel counters and an occasional element of conduit.
There are five options:
- A one-story studio, 309 to 589 square feet
- A one-story one-bedroom, 534 to 794 square feet
- And a one-story two-bedroom, 1,200 square feet
Fung + Blatt Architects
Fung + Blatt Architects is a Los Angeles-based firm founded in 1990.
The city has approved its 795-square-foot, one-story, one-bedroom unit with a roof deck. It estimates the construction cost to be $240,000 to $300,000, excluding landscape, site work and the solar array. Homeowners can also expect other additional costs.
Taalman Architecture/ IT House Inc.
The design team behind "IT House" is Los Angeles-based studio Taalman Architecture. Over the past 15 years, IT House has built more than 20 homes throughout California and the U.S.
The IT House ADU standard plans include the tower, bar, box, cube, pod and court.
The city has approved four options, including:
- A two-story including mechanical room, 660 square feet
- A two-story including mechanical room, 430 square feet
- A one-story studio, 200 square feet
- A one-story including mechanical room, 700 square feet
The firm also has another two projects pending approval: a 360-square-foot one-story studio and a one-story, three-bedroom at 1,149 square feet.
LA Más
LA Más is a nonprofit based in Northeast Los Angeles that designs and builds initiatives promoting neighborhood resilience and elevating the agency of working-class communities of color. Homeowners who are considering their design must commit to renting to Section 8 tenants.
The city has approved two of LA Más' designs: a one-story, one-bedroom, 528 square feet unit and a one-story, two-bedroom, 768 square feet unit. The firm has another design for a one-story studio pending approval. That design would be the first 3D-printed ADU design in the city's program.
Jennifer Bonner/MALL
Massachusetts-based Jennifer Bonner/MALL designed a "Lean-to ADU" project, reinterpreting the stucco box and exaggerated false front, both Los Angeles architectural mainstays.
The design has been approved for a 525-square-foot one-story, one-bedroom unit with a 125-square-foot roof deck.
sekou cooke STUDIO
New York-based sekou cooke STUDIO is the sole Black-owned architectural firm on the project.
"The twisted forms of this ADU recalls the spin and scratch of a DJ's records" from the early 90s, the firm said.
Its design, still pending approval, is for a 1,200-square-foot, two bedroom and two bathroom can be adapted to a smaller one-bedroom unit or to include an additional half bath.
SO-IL
New York-based SO-IL was founded in 2008. It has completed projects in Leon, Seoul, Lisbon and Brooklyn.
Its one-story, one-bedroom 693-square-foot unit is pending approval. It is estimated the construction cost will be between $200,000 and $250,000.
WELCOME PROJECTS
Los Angeles-based Welcome Projects has worked on projects ranging from buildings, houses and interiors to handbags, games and toys.
Its ADU is nicknamed The Breadbox "for its curved topped walls and slight resemblance to that vintage counter accessory."
It has been approved for a one-story, one-bedroom 560-square-foot unit.
wHY Architecture
Founded in 2004, wHY is based in Los Angeles and New York City. It has taken on a landmark affordable housing and historic renovation initiative in Watts.
Its one-story, one- or two-bedroom 480 to 800-square-foot unit is pending approval.
Firms that want to participate in the program can learn more here . Angelenos interested in building a standard ADU plan can learn more the approved projects here.
From Your Site Articles
- United Dwelling Raises $10M to Address the Housing Shortage ... ›
- Plant Prefab Raises An Additional $30 Million - dot.LA ›
- How 3D Printing Could Help Tackle Homelessness in LA - dot.LA ›
- New Bills, New Startups Address Housing in California - dot.LA ›
- LA's ADU Culture Still Faces Financial Barriers - dot.LA ›
- What Will Take To Make Modular Homes Mainstream? - dot.LA ›
Related Articles Around the Web
Sarah Favot
Favot is an award-winning journalist and adjunct instructor at USC's Annenberg School for Communication and Journalism. She previously was an investigative and data reporter at national education news site The 74 and local news site LA School Report. She's also worked at the Los Angeles Daily News. She was a Livingston Award finalist in 2011 and holds a Master's degree in journalism from Boston University and BA from the University of Windsor in Ontario, Canada.
Behind Her Empire: How Camping World CEO Marcus Lemonis Lives Out His 'Mother's Mission'
04:08 PM | July 23, 2021
Marcus Lemonis
On this episode of the Behind Her Empire podcast, hear from Marcus Lemonis, the CEO and chairman of the multi-billion dollar business Camping World and the host of CNBC's "The Profit."
Lemonis is the first male guest on Behind Her Empire, but prioritizing diverse entrepreneurship remains the theme for this episode. Lemonis says he is constantly inspired by his mother who "always felt… that women rule the world."
He says he's made his mother's values a cornerstone in his work, which is centered around "living out my mother's mission." To Lemonis, this means "creating platforms and creating pathways that allow women and women of color and people of color… to be given opportunities that have been… not made available to them."
To achieve this, he created The Lemon-AID Foundation, focused on backing underrepresented founders, which he seeded with $50 million of his own money.
Lemonis says he prefers to work with female founders because he "think[s] that women, generally speaking, don't make decisions with their ego." He also shares how he thinks "women make better business people because they also manage with a level of empathy."
Lemonis also shares his strategies for overcoming the fear of embarrassment, something he feels everyone has to deal with. He argues that by giving yourself permission to be embarrassed, you give yourself permission to fail, and fail with dignity.
In the rest of the conversation, Marcus shares how he got started with entrepreneurship, how he avoids imposter syndrome and how he dresses to feel free.
Marcus Lemonis is the CEO and chairman of Camping World, and the host of "The Profit."
"Ultimately, businesses are run by people... Whether you're running Dell computers, or Susie's coffee shop, the numbers may have more commas in them. But it really doesn't change the principles." —Marcus Lemonis
dot.LA Engagement Intern Colleen Tufts contributed to this post.
Want to hear more of the Behind Her Empire podcast? Subscribe on Stitcher, Apple Podcasts, Spotify, iHeart Radio or wherever you get your podcasts.
From Your Site Articles
Related Articles Around the Web
Read moreShow less
Yasmin Nouri
Yasmin is the host of the "Behind Her Empire" podcast, focused on highlighting self-made women leaders and entrepreneurs and how they tackle their career, money, family and life.
Each episode covers their unique hero's journey and what it really takes to build an empire with key lessons learned along the way. The goal of the series is to empower you to see what's possible & inspire you to create financial freedom in your own life.
Los Angeles’ Top Startup Incubators and Accelerators
06:00 AM | December 30, 2021
Snap Yellow accelerator program heads\u00a0Alexandra Levitt (left) and\u00a0Mike Su.
Whether you are making medical devices or movies, if you have a promising startup chances are there’s someone out there to help.
Southern California is home to an armada of accelerators, incubators, startup studios and other programs designed to help new business owners develop their vision and launch the next billion-dollar business.
Some of these programs are run by investors, who often go on to back the companies they incubate in later rounds. Others were created as a way for existing companies like the Walt Disney Co. or the Los Angeles Dodgers baseball team to mine talent in their backyard for future revenue opportunities. Programs like the LA Cleantech Incubator target companies from across the globe that are developing tech to mitigate the climate crisis.
While some accelerators opt to provide funding outright in exchange for an equity stake, some prefer to not financially invest, and instead offer founders a place to work, access to mentors, and a full calendar of networking opportunities to help them connect to investors who might look to cut a check.
Local companies that grew from accelerators include Dollar Shave Club, which began at Mike Jones’ Science Inc. in Santa Monica and was sold to Unilever for $1 billion in 2016. Bill Gross’ Pasadena-based IdeaLab has also led several startups to big exits, including crypto exchange Coinbase which was valued at $80 billion when it completed an IPO this April.
Most of these accelerators accept applicants from both in and outside LA County, and some offer virtual workshops. Here’s a list of the top programs in LA that are helping new startups get off the ground.
GENERAL TECH ACCELERATORS
AmplifyLA’s accelerator backs early-stage companies that are local to L.A. County. Besides funding them through its accelerator, it works with startups in all industries to connect them to a network of L.A.-based startup founders and investors to raise additional funding once they leave the program. Notable past companies that used AmplifyLA include wine subscription firm Winc and on-demand moving and storage company Clutter.
Location: Venice Beach
Type of Funding: Pre-seed, early stage
Focus: Software, emerging technology companies, D2C brands
Serial entrepreneur Bill Gross founded IdeaLab in 1996, and it’s since backed over 150 companies and seen 45 of those either go public or be sold. IdeaLab backs companies regardless of their growth stage or industry but has a history of backing tech companies focused on environmental or social change. Success stories include robotics firm Elementary, crypto exchange Coinbase and GIF database Tenor.
Location: Pasadena
Type of Funding: All stages, focus on seed and early stage
Focus: Agnostic, focused on any tech company
Techstars is a global outfit with a chapter in Los Angeles that opened in 2017. It prioritizes local companies but will fund some firms based outside of L.A. Director Matt Kozlov said Techstars L.A. looks to fund a wide range of companies but does try to target ones working in industries that are strong in L.A., like healthcare, artificial intelligence, e-commerce, retail, property tech, software as a service, and consumer tech.
Location: Downtown Los Angeles
Type of Funding: Pre-seed, seed rounds
Focus: Aerospace, energy, robotics, wellness, entertainment, mobility/logistics, education
Notable Companies: Sanity Desk, Lightbox
Grid110 offers founders two programs: a 12-week residency program for early-stage startups in L.A. that haven’t launched yet, and another 12-week ‘friends and family’ program run in partnership with L.A.-based venture firm Slauson & Co. that offers a $20,000 grant and course aimed at “demystifying funding” and guiding founders. Unlike some accelerators on this list, Grid110 doesn’t require an equity stake in a company in exchange for participating.
Location: Downtown Los Angeles
Type of Funding: Early stage, seed
Focus: Agnostic, focused on any tech company
Notable Companies: Rent a Romper, Struct Club
Michael Jones’ Science is a venture capital firm focused on funding early stage startups, and it also runs a venture accelerator that’s incubated some big direct-to-consumer brands, including Dollar Shave Club and PlayVS. Founders work out of Science’s campus in downtown Santa Monica where they collaborate with Jones and other entrepreneurial mentors as well as a staff of marketing, tech, and business development professionals to get their idea off the ground. Usually, Science contributes these services in exchange for a board seat and/or equity in a startup.
Location: Santa Monica
Type of Funding: Early stage VC, seed rounds
Focus: Mobile companies, direct-to-consumer, marketplace and e-commerce
Notable Companies: Dollar Shave Club, Liquid Death, PlayVS, Arrive
Santa Monica-based VC Mucker Capital also runs Mucker Lab, its accelerator for startups that are either in their earliest stages of development or looking to grow by spinning off a business unit or revamping their strategy. It invests in an array of tech companies but prefers direct-to-consumer businesses. There’s no set duration for its program, but most founders work with Mucker for at least a year. Mucker invests between $100,000 and $175,000 in companies in exchange for an 8% to 15% equity stake.
Location: Santa Monica
Type of Funding: Pre-seed, or spin-off
Focus: Agnostic, focused on any tech or direct-to-consumer company
Notable Companies: ServiceTitan, Trunk Club, Honey
Law firm Stubbs Alderton & Markiles founded its six month preccelerator program to provide startups with access to other valuable resources besides funding -- including workshops, mentorship and a package of legal services and perks it estimates is worth $500,000. Notable alumni include location-based marketing startup Rally.
Location: Santa Monica
Type of Funding: Doesn’t contribute funding, provides networking, mentorship and legal services
Focus: Agnostic, focused on any tech company
MEDIA & ENTERTAINMENT
One of the world’s largest entertainment companies, Disney is always on the hunt for new investments that can enhance its growing streaming, parks and entertainment businesses. It accepts growth-stage startups that are looking to use tech to change the entertainment industry and runs a three-month summer program that culminates in a demo day in October. Disney will invest in these startups in addition to co-working space in L.A. and mentorship from Disney executives. Though Disney often plans to strike deals to use some startups’ tech in its business, companies that develop IP during the accelerator retain full ownership of it.
Location: Burbank
Type of Funding: Growth stage, venture-backed startups encouraged
Focus: Media/entertainment, streaming, social media, kids’ entertainment
Notable Companies: Epic Games, Holler, Caffeine
Snap Inc.’s Yellow accelerator is a 13-week program for startups developing anything that could enhance digital entertainment, including direct-to-consumer brands, new social apps, creative tools or augmented reality experiences. Snap invests up to $150,000 in each startup and provides a network of creative industry executives as mentors. It invests with the aim of using startup tech in future Snapchat or Snap Inc. projects.
Location: Santa Monica
Type of Funding: Stage agnostic
Focus: Companies at the “intersection of creativity and technology”
AEROSPACE
Starbust Aerospace Accelerator
The Starburst Aerospace Accelerator connects aerospace and defense startups with a network of mentors that help them fundraise and hire. It’s also a way for startups to gain inroads to potentially valuable contracts with the U.S. Department of Defense, which is always looking for the next SpaceX. The company also partners with UCLA's school of engineering to offer a 13 week Scale accelerator program, aimed at seed and pre-seed startups.
Location: Los Angeles
Type of Funding: Doesn’t contribute funding, provides networking, mentorship, fundraising help
Focus: Aerospace, defense
Notable Companies: SeaSatellites, Pierce Aerospace
SPORTS
Los Angeles Dodgers Accelerator
Founded in 2015 as a partnership between R/GA Ventures’ Global Sports Venture Studio and the L.A. Dodgers, this program provides up to $120,000 to local sports-focused startups in exchange for up to 6% equity. Originally for a limited time, the outfit expanded to be a year-round program in 2018.
Location: Los Angeles
Type of Funding: pre-seed, seed
Focus: Sports tech, food and beverage, sports entertainment
Notable Companies: Appetize, ShotTracker
FOCUSED ON STARTUPS BY PEOPLE OF COLOR
Movember is a men’s health charity that encourages people to grow mustaches in November to raise awareness of suicide prevention, testicular and prostate cancer, but it recently launched the Rooted & Rising division to invest in creators. Rooted & Rising backs young Black creators who are creating culture-shifting art and provides them with a network of like-minded mentors and in exchange for creating up to three pieces of content during the three-month program.
Location: Los Angeles
Type of Funding: Individual funds, up to $5,000 each
Focus: Creatives of color
The Starfish Accelerator was created this year to give creative people of color funds and mentorship to create projects. Backed by the Doris Duke Foundation, participants are given a $50,000 grant and access to several mentors for six months to produce their work.
Location: Los Angeles
Type of Funding: Individual funds, up to $50,000 each
Focus: Creative IP, creatives of color
Expert Dojo is an international group with a cohort in Santa Monica. It prioritizes backing women-led startups and companies run by people of color. It invests an initial sum of $25,000 to $100,000 in participating pre-seed and seeded startups, and often invests in follow-on rounds up to $1 million. Local success stories include travel app Elude and influencer booking site Mavens List.
Location: Santa Monica
Type of Funding: Pre-seed, seed
Focus: Tech companies led by women and/or people of color
CLIMATE & CLEAN TECH
LACI’s goal is to fund startups that are both local and global that will create technologies to mitigate the effects of climate change and create greener, smarter cities. It runs several programs including a two year-long incubator where companies work out of its Downtown LA office, and invests in up to 50 startups each year.
Location: Arts District
Type of Funding: Pre-seed, seed, Series A and B
Focus: Clean energy, renewables/sustainability, solar, smart cities
COLLEGE/UNIVERSITY-RUN PROGRAMS
UCLA Anderson Venture Accelerator
UCLA’s venture accelerator is a four-month program that has incubated over 70 companies, which have raised $144 million in funding. Led in part by entrepreneur in residence Rod Kurtz, it helps student and faculty entrepreneurs bring their ideas and research to market.
Location: Westwood
Type of Funding: Doesn’t contribute funding, provides networking and mentorship opportunities
Focus: Agnostic, focused on any tech company. Student, faculty and alumni startups preferred.
Notable Companies: UNest, KPOP Foods
USC’s startup accelerator’s next cohort begins in Spring 2022. It doesn’t take equity, but also doesn’t offer funding -- instead connecting founders with potential investors snad giving them hands-on guidance and access to coworking space.
Location: Marina del Rey
Type of Funding: Doesn’t contribute funding, provides networking and mentorship opportunities
Focus: Deep Technology, Machine Learning and AI. Student, faculty and alumni startups preferred.
HEALTH, WELLNESS & BIOTECH
Founded in 2015, Cedars-Sinai Hospital’s three-month program gives companies up to $100,000 in funding and access to mentors both on the executive and medical sides of the business. It prioritizes startups looking to innovate in patient care, cybersecurity, genetics, machine learning and medical devices.
Location: West Hollywood
Type of Funding: Early/growth stage, seed, Series A.
Focus: Healthcare, Information management, Medical technology
Notable Companies: AppliedVR, CancerAid
CITY & COUNTY-RUN PROGRAMS
Created by Mayor Eric Garcetti in 2016, this program is a nonprofit that supports local businesses with mentorship and networking for funding. Applicants must be based in L.A. County, and all areas of tech are accepted.
Location: Greater Los Angeles
Type of Funding: Doesn’t contribute funding, provides networking and mentorship opportunities
Focus: Hardware, food and agriculture, healthcare/biotech, mobility, aerospace, manufacturing
Founded and fully supported by the City of Long Beach, this accelerator provides seed funding and mentorship and also helps companies plan exit and acquisition strategies. Run by managing director Andrea White-Kjoss, the four-month program gives founders access to $75,000 to $100,000 in exchange for 6-7% equity. The accelerator launched as digital only, but is planning an in-person component soon, pending COVID regulations.
Location: Long Beach
Type of Funding: seed
Focus: Tech startups located in Long Beach
An earlier version of this post also listed the Techstars Aerospace Accelerator, which is no longer in operation.
From Your Site Articles
- USC Granted $15 Million For Tech Startup Incubator - dot.LA ›
- Startup Co-Living Concepts Are Booming in LA - dot.LA ›
- Brazen Bio Incubator Wants to Build More Scientist CEOs - dot.LA ›
- KPOP Foods Acquired By Korean Food Retailer Wooltari USA - dot.LA ›
- ServiceTitan Files for IPO at a Reported $18B Valuation - dot.LA ›
- LA Is The Third-Largest Startup Ecosystem in the U.S. - dot.LA ›
- These SoCal Startups Get Ahead of the Game Via Comcast’s Sports Tech Accelerator - dot.LA ›
- Long Beach Accelerator Set to Welcome Fourth Group of New Companies - dot.LA ›
- RYZ Labs Wants To Be a 1-Stop Shop for Startups - dot.LA ›
- Billie Jean King, Dodgers Partner on a New Accelerator - dot.LA ›
- Nobody Studios Plans to Build 100 Startups in Five Years - dot.LA ›
Related Articles Around the Web
Read moreShow less
venture capitalamplifylaidealabtechstarsgrid110science incmuckerlabsam precceleratordisneysnapla cleantech incubator
Samson Amore
Samson Amore is a reporter for dot.LA. He holds a degree in journalism from Emerson College. Send tips or pitches to samsonamore@dot.la and find him on Twitter @Samsonamore.
https://twitter.com/samsonamore
samsonamore@dot.la
RELATEDTRENDING
LA TECH JOBS