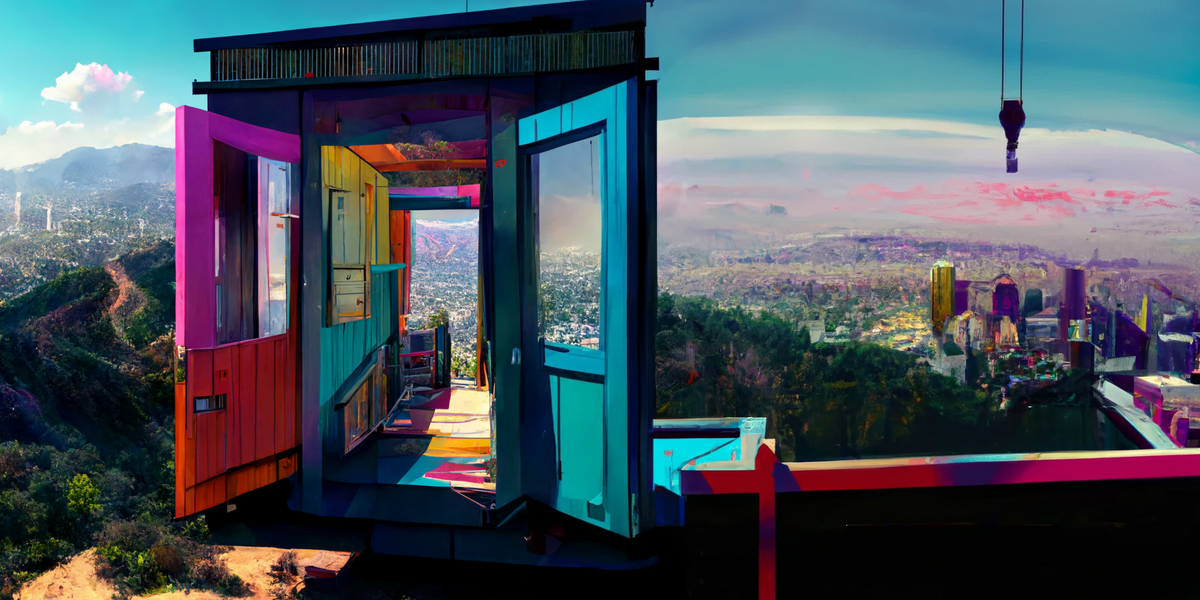
This is the web version of dot.LA’s weekly newsletter. Sign up to get the latest news on Southern California’s tech, startup and venture capital scene.
Not all that long ago, “pre-manufactured” or modular homes were typically found in places like trailer parks. Though certainly some nicer and more upscale versions of the concept existed, the stigma around the idea of moving into “prefabricated housing” has, nonetheless, lingered in the American consciousness.
That may be on the verge of changing, thanks to a number of economic and social changes that have made sweeping changes to the US housing market and placed new barriers to entry in front of millions of workers and potential homeowners. A combination of long-term wage stagnation, a looming recession, rising student loan debt, and in particular, skyrocketing real estate prices have put homeownership out of the reach of much of the active labor force, particularly among young people. For many, the choice isn’t between a prefabricated home or conventional home ownership, but a prefabricated home and an indefinite future as a renter.
Fortunately, technological innovations – particularly in the realm of 3D printing – make today’s modular housing options more attractive than in years past. Unlike conventional “stick-built” homes, in which the entire property is contained within a unified wood frame, modular homes are pre-built in sections off-site and then fit together on top of a permanent foundation, making them far easier to break down, transport, and re-create elsewhere.
The Pros
Obviously, the greatest single advantage of the modular approach is cost. Because they’re put together indoors in a factory setting, with multiple units being assembled side-by-side, modular homes are far faster and cheaper to construct by square foot than their traditional counterparts. While stick-built homes can run $200-$500 per square foot to build, many modular home companies can bring costs down to closer to $60-$80 per square foot, a considerable savings. On top of those initial savings, homes that are built atop a permanent foundation – even modular homes – tend to appreciate and depreciate more than permanent “stick-built” homes than mobile homes or trailers.
There are, of course, other benefits as well. Modular homes use less energy to build, and they’re made with materials that are easier to recycle rather than ending up in landfills. Many states even offer “green” tax credits for modular home buyers.
One other hidden benefit? Pre-approval for innovative home designs and features. For example, Los Angeles homeowners who want to add a “granny flat” – a small self-contained dwelling – on their property typically have to navigate a confusing sea of bureaucracy and red tape. But a number of local prefabricated home designers have had “granny flat” designs pre-approved for installation around the city. Some local activists and urban planners have even theorized that these kinds of accessory dwelling units – or ADUs – could be a key tool in solving the city’s housing crisis.
...And Con
Despite its numerous advantages, the prefabricated housing trend has yet to go fully mainstream. Only around 2% of single-family homes built in 2021 were modular. But it’s still relatively early days, and Southern California’s particularly high labor and building costs make the concept particularly attractive, turning the region into something of a hub for this nascent industry.
The Players
Culver City’s Azure Printed Homes 3D prints backyard studios, granny flats, and other ADUs out of recycled polymer plastic. A 120-square-foot studio space runs just $24,000, not including delivery fees and optional add-ons like solar panels or air conditioning. The entire process – from initial order to final installation of the product – takes just one week, with the structures themselves typically fashioned in under 24 hours.
Modular backyard home designer Cover works with a particular blend of construction materials and layouts to customize its homes for Los Angeles’ Mediterranean climate and sunny year-round weather. A tiny backyard home the company installed in Highland Park is a particularly compelling example of how these homes can be designed to suit their ultimate environments.
One of the leaders in the local modular housing space is Plant Prefab, which already has two operational factories and recently raised $42 million in additional funding to begin work on a third. While most modular home companies have focused on conventional single-family designs that can be easily replicated for different settings and communities, like Cover, Plant Prefab works with architectures to prefabricate more specific, localized designs that are customized for their eventual location. Unlike many other rivals, the company also constructs its homes with basic infrastructures – like electrical and plumbing systems – built in, cutting down on the complexity of the post-installation but pre-move-in phase and making the final results more precise.
Santa Monica’s Minarc created mnmMOD, a wood-free prefabricated wall system made from extruded polystyrene and 30% recycled steel. The material cuts down on heat loss, saving money on electrical bills, it’s free of many of the volatile chemicals and gasses that maintain and power US homes – known as VOCs –and it’s resistant to fire, mold, and warping over time. Marina del Rey’s Sander Architects have spearheaded an innovative new building method, known as “hybrid construction,” which combines the ease and efficiency of modular home building with the customization of more conventional approaches.
Another fascinating local take on the trend comes from CRATE Modular, which converted shipping container units into housing complexes for people experiencing homelessness. The first such complex was completed in April 2021 in Downtown Los Angeles; within one month of installation, every room was occupied.
It’s unlikely that any one trend or innovation on its own will solve big-picture problems like Los Angeles’ housing crisis. Still, signs point to prefabricated housing as one potential way forward to make new construction more affordable and efficient, as well as make housing generally more accessible to thousands of Angelenos. - Lon Harris
Prediction: The Future of AI is Influencer Marketing
In 2023, artificial intelligence (AI) will continue to accelerate and make its way into a sector in which far fewer people are considering its impact: the creator economy.
Prediction: EVs Are Disrupting Car Shopping Habits
As consumer interest in electric vehicles has grown, EV-curious consumers are becoming more open to moving away from the brands they’ve come to trust—a huge opportunity for companies that can deliver stylish, low-cost electric vehicles quickly.
What We're Reading...
- Vinfast will be showing their VF6, VF7, VF8, VF9 models at CES, though considering the recent bait-and-switch on the only models delivered to US customers, take it with a grain of salt.
-A geoengineering startup Making Sunsets has begun distributing particles into the atmosphere via hot air balloons in an effort to 'tweak' the climate, which has some MIT scientists asking "Maybe...don't?"
- Google may lay off 6% of its workforce in 2023 under the guise of poor performance reviews.
- Did Twitter have the data of 400 million users compromised by a threat actor? If the previous 361 days are any indication...probably?
--
How Are We Doing? We're working to make the newsletter more informative, with deeper analysis and more news about L.A.'s tech and startup scene. Let us know what you think in our survey, or email us!